By: Lee Williams
Taking a deeper look at the costs associated with live edge products.

When we were first starting Sovereign and getting into live edge design and epoxy pours, a part of our job was to do market research. Davia and I would spend countless hours poring over Etsy, Wayfair, and other shopping sites, trying to settle upon an amount we could charge our customers that wasn't too far above the market rate to lock in jobs... But also not too far below the going rate to make as much profit as possible-while still considering our consumer. We went through a lot trying to nail down this elusive number: we got quotes from other makers, researched on blogs, watched Pricing videos, and went through every other channel we could. And somehow, when we looked at the market, it still was difficult to get a serious grip on a steady pricing structure for live edge pieces.
If you've been live edge shopping, you've experienced the same: some makers claiming that they do pieces for under $1,000, while others may want more than triple or quadruple for the same exact design. This fluctuation in price for what is being advertised as comparable value confuses buyers, and can discourage them from purchasing in this style. We experienced the same confusion when we started in the market, and we want our patrons and members to know why this fluctuation exists, and how to settle upon the price they are willing to pay to add live edge to their aesthetic.
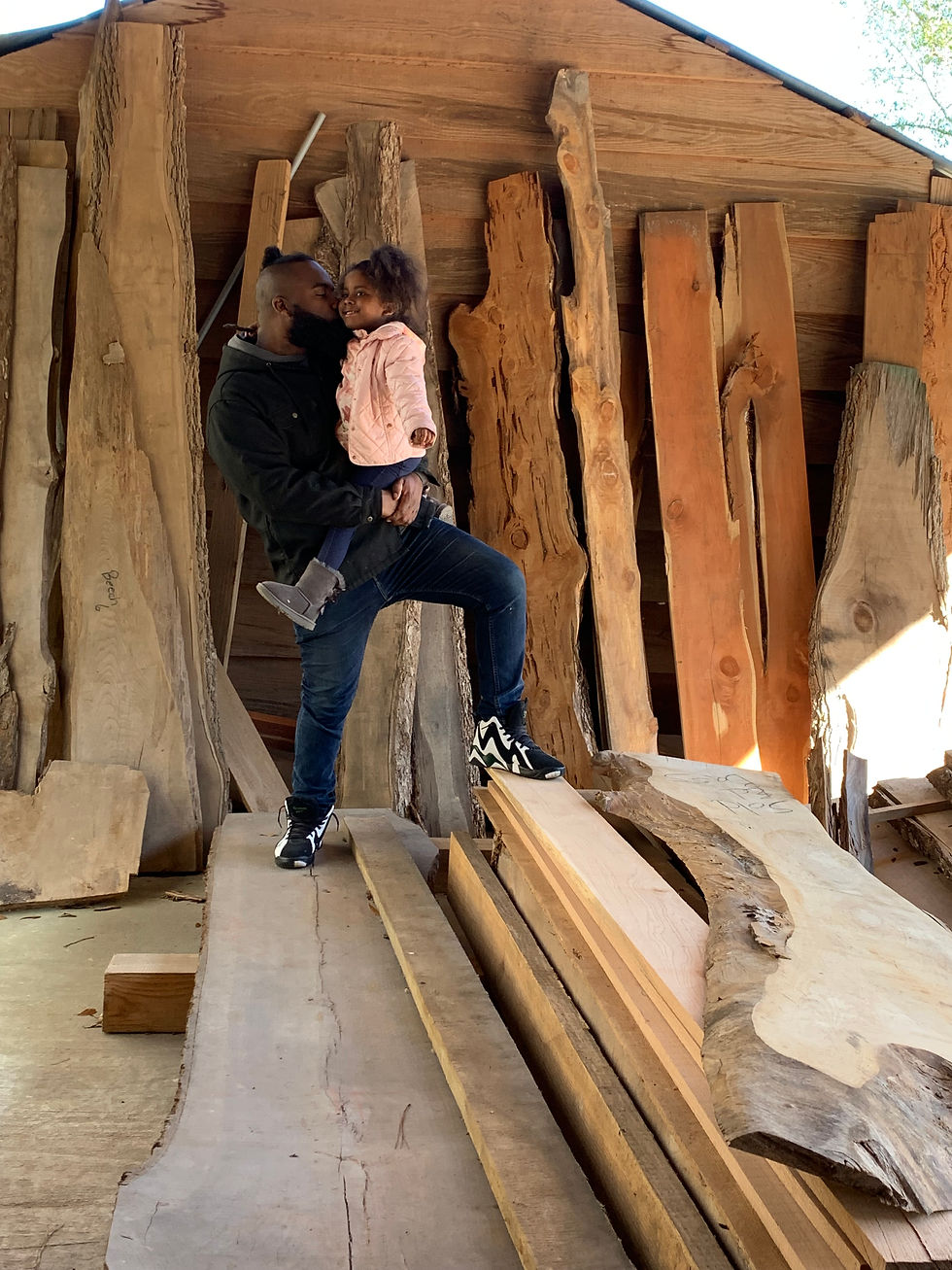
After researching like tourists on vacation, we settled in on this. Our final conclusion became that live edge costs are dictated by factors that vary greatly. Because of this, the price of the pieces also varies equally as much. A lot is involved with the completion of a live edge project, and if a maker is working with limited space or equipment, this may cause them to charge more. A maker that has a better or more feasible setup may charge less, because it does not take the same time and effort to get the job done. Just as space and equipment weigh in on price, so do other factors, like size of the company, storage, sanding, finishing, curing, shipping, handling, and even insulation come into play.
Here, we will compile all of what we've learned from observing and being involved in the industry, and reveal what factors we use to determine pricing for our own custom live edge projects. This blog will be useful for our clients, other makers, and buyers in the market that simply want to understand the difference between a $600 live edge table, and a $16,000 one.
Let's start at the beginning. The first order of business is to determine the price of the slab, according to dimensions of the finished product.
The average person would probably think that a maker can just go outside with a chainsaw, cut down a tree, cut it into a cool-looking design, put it on some legs, and put it inside the house, and Voila!- that's live edge. This is not the case at all.
It is important for the raw slab to air dry, kiln-dry, and be processed. This procedure, when done properly, can take up to a year; so your maker can't just go to the mill and pick any slab of wood they have to make your piece. They're looking to pick a piece that qualifies procedurally as well as aesthetically.
Also, the slabs aren't normally sold completely flat from the mill, and even if they are available that way, you'll pay for the service. For instance, at our mill, we can get a 2 inch thick, 8 foot long unfinished slab of red oak for $2-300. But with this slab, we have to do everything- debark, debug, plane, route, sand, treat, and process the wood. If we order one online from a distributor that does all of this first, the same slab can easily cost $800 or more- not to mention that we have to have it shipped to our location, which costs even more.

If your mill doesn't make these services available (ours doesn't, other than kiln-drying), your slab will have to go through the same process, and will also have to be cut to fit the design's specifications depending on the type of piece being made. For instance, live edge epoxy river tables usually require a rip cut down the middle of the slab and a cut down each end at a 90 degree angle to the long cut, which eventually creates the table's corners. The maker is charging you for having the vision and expertise to make these cuts properly, to the size specifications, in a way that will not ruin the end result and require the purchase and processing of another slab.
Quick recap: Milling, Kiln-drying, flattening, and processing the slab are all services that your maker may or may not do themselves prior to completing your project, depending on their capability and the size of their makerspace or workshop. If they do not complete these services themselves, then they are each a service that has to be paid for, and may not all be able to be completed by the same source. If the maker is paying for the services, this will affect the price they charge you.

Now that you understand the process your wood is about to go through, what factors of the wood itself make it more valuable? The price of a live edge slab from the mill varies depending on many factors including size, anomalies (we call these "beauty marks" and we're referring to knotting, spalting, splitting, and voids that make a slab more attractive), type of wood, its abundance in the general area of the build, choices of finishes and stains, age and history of the tree the slab comes from, general milling costs in the area, and more. And you want to be very detail-oriented, because the process can get pretty detailed.
For example, I learned from doing these projects that if a client falls in love with a slab, but its porous from previous insect burrows, I might need to charge more because I have to watch a porous slab more closely, and over a longer period of the drying/curing time. This is because the holes create tiny bubbles that can easily become permanent in the glaze coat if they're not watched and attended to during the pour. I learned that I should charge more for spalted slabs, because they must be reinforced and the epoxy has to be poured differently... and if spalted slabs are not being covered with a food-grade glaze coat, they need to be treated to be safe to eat on. These are factors that I would have never thought of being significant, until I came across these issues while pursuing the craft.
All things considered, if you're just looking for an average priced slab, unfinished live edge wood slabs average about $20 per board foot, which is a wholesale price by current market standards.
One reason these slabs are relatively expensive is because of their unique nature. The wood is more rare, if you're comparing slab to plank boards purchased in bulk. Sourcing slabs can be costly. The rule of supply and demand naturally kicks in to raise the market prices of these products.
Another driving factor of pricing from a maker to a client is the transport of the slab. Live edge slabs are usually purchased from a mill or tree service near the maker's studio or space. If this is the case, and the mill doesn't have a kiln, the maker is responsible for kiln drying. If they are, this means that they have to transport the slab to the kiln and then to the shop once dry. However, most reputable mills that sell slabs have a kiln on the property. If there is a kiln, the slab needs to be picked up after its dry and transported to the makerspace. Either way, this adds to the price charged to the client. And judging by gas prices lately... The price may be going up.
Once it's transported, it has to be stored until your project is started. If the maker runs a small but busy shop like ours and has clients before you, storing your slab may take up a good amount of their space. For every spot that is taken by a slab, another job that the maker could take on today gets pushed back, and anything that causes a maker to take longer to complete work or have to push a current inquiry back on their estimated completion date is a chargeable expense to the client who the service is done on behalf of.
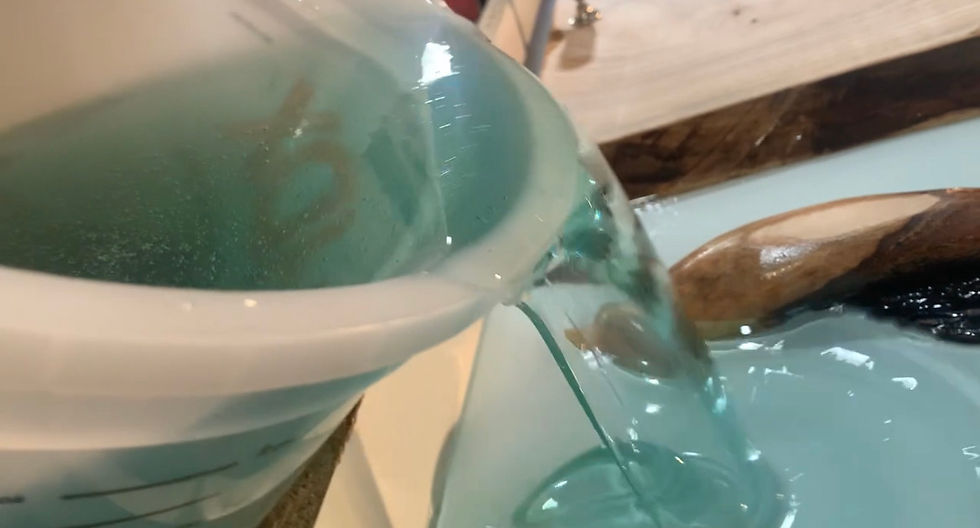
Epoxy also takes time to be poured and dry, and it needs a particular humidity, temperature, and clean conditions to cure properly. A maker has to provide these conditions in his shop, and place the piece in a completely static position where nothing can affect it as it dries and cures. The maker is charging you for this time as well, especially if it is someone like myself, that does FAR more than just epoxy. I'm working with 700 square feet, and if I have a large epoxy job curing in my space, I can't do anything inside until its dry. This creates a timeframe where my shop, which is my only source of income, is inaccessible. So obviously, this is something I have to consider when pricing a job.
All of these are considerations we make BEFORE getting to the general pricing of epoxy. The type of epoxy needed depends on what depth the epoxy will be poured, and what the surface will be used for. For countertops, bars, coffee tables, and dining tables, its important that the top coat is food safe. For River tables, it's important that the 2 inch thick river being poured is made of deep pour epoxy (formulated for pours 1 inch thick or more).
Your maker is responsible to know how much epoxy your job requires and why. They should already have a partnership or a connection with an epoxy distributor/manufacturer that provides a consistent and dependably high-performance product. We love to work with Stone Coat Epoxy products, and sometimes we use Liquid Glass. There are calculators online that will help you to judge the amount of epoxy needed for a particular thickness of pour, but only a professional eye can really verify these amounts based on every factor that determines dimension.
Deep pour epoxy is about $175 per 1.5 Gallon kit, and Glaze Coat is about $80 per gallon. To give you an idea of the expenditures involved, a 6 foot Dining table that we did recently required 6-7 gallons of deep pour epoxy.
Now that your maker has your slab, fully dried, cut, and processed, and has figured out the amount it will cost for the epoxy to pour your piece, what are they supposed to pour this epoxy into? A form, of course. The form is made of melamine, screws, caulk, and tuck tape. The price for the form to be built depends on the size of the project.

If you're getting a table of any kind, it is important for your maker to ask you what type of base you want to hold your table up. We make and manufacture any kind of base for our clients right in our shop. We weld our own metal legs, and we've had clients ask for bases made of a tree trunk, concrete, or wood as well. We are willing to do it all, but it comes at a cost- which is probably best to consider upfront, while you're counting all the other costs involved.
There are also some knickknacks that your maker will need to get the job done. Release spray is one of the most important, because it ensures that the epoxy, which has cured inside of the mold, will release from the mold after the piece is complete. Also, your maker will need buckets, pour pitchers, stir sticks, spreaders, squeegees, gloves, tarps to catch drips, and sandpaper. We usually apply these to the estimate as a fixed "shop fee," but if your maker is worth their weight, they're factoring these expenses in, no matter what they're calling them.
If you are a local client to the maker producing your project, then they have to deliver it to you. I help local clients with assembly, but I'm pretty sure there are makers out there who do not. If they don't, we're hoping they'd at least include some very effective instructions on how to attach your top to its base. If you are a client receiving a shipping order, your maker has to build a shipping crate. This crate, although its just a glorified wood box, needs to be outfitted with an insulated interior to protect the surface of the table top from weather, temperature, and unwanted movement that could result in scratching or damage during transport. The cost of this crate also varies based on the size of the project being shipped. The crate adds weight to the overall shipping assembly, which adds to the shipping costs.
While shipping large pieces, we have come across the issue of needing to lift long crates onto our freight partner's trucks. There is a forklift especially made for this function, but its costly for the freight company to bring out that particular lift. Some pieces I've seen lifted by 2 trucks' lift gates simultaneously because they were so large. When these types of accommodations are necessary on the pickup and receiving end to get your piece on and off of the transport vehicle, it becomes more understandable why shipping your live edge conference or 12-seater dining table may be so expensive.
Last but not least, it's easy for you to read the article about the process, but it's much harder for your maker to complete the process, all the time, every day, in a dependable format. How much are you willing to know that your maker took home, now that you know all of the work they have to do on your behalf? The labor cost is all up to the maker, and everyone has their own formula, based on their company location, shop conditions, freight costs, and market value. We here at Sovereign ship nationwide, and are prepared for any project, because we know what to do with our small space, and where to go if we need a larger one. Depending on where you are, sometimes its worth it to get a maker from a different area to deliver. If the expertise level is higher, they'll be accounting for every factor before the job commences. If you go for the cheap price, it could end up costing you dearly down the line.
In conclusion, To give clients an easier gauge of our product pricing, for the average live edge epoxy river dining table (3’ wide and 2” thick) we charge about $640 per linear foot. We feel like this is a competitive place to sit in the market, and it accounts for what we have to do as makers to consistently manufacture the best product. Contribute to the makerspace of your choice by making your order, and now that you've made it through this quick pricing article, you'll know exactly what your paying for.

Mastodon: The Sovereign Way is a subsidiary content provider of Sovereign Customs X Design, INC. We post new blogs twice a week about our Makerspace, Creating Custom pieces, Sovereignty, Self-Sufficiency, Off-Grid Living, Hunting, Guns, Motors, and Martial Arts. Visit us at sovereigncustoms.com
コメント